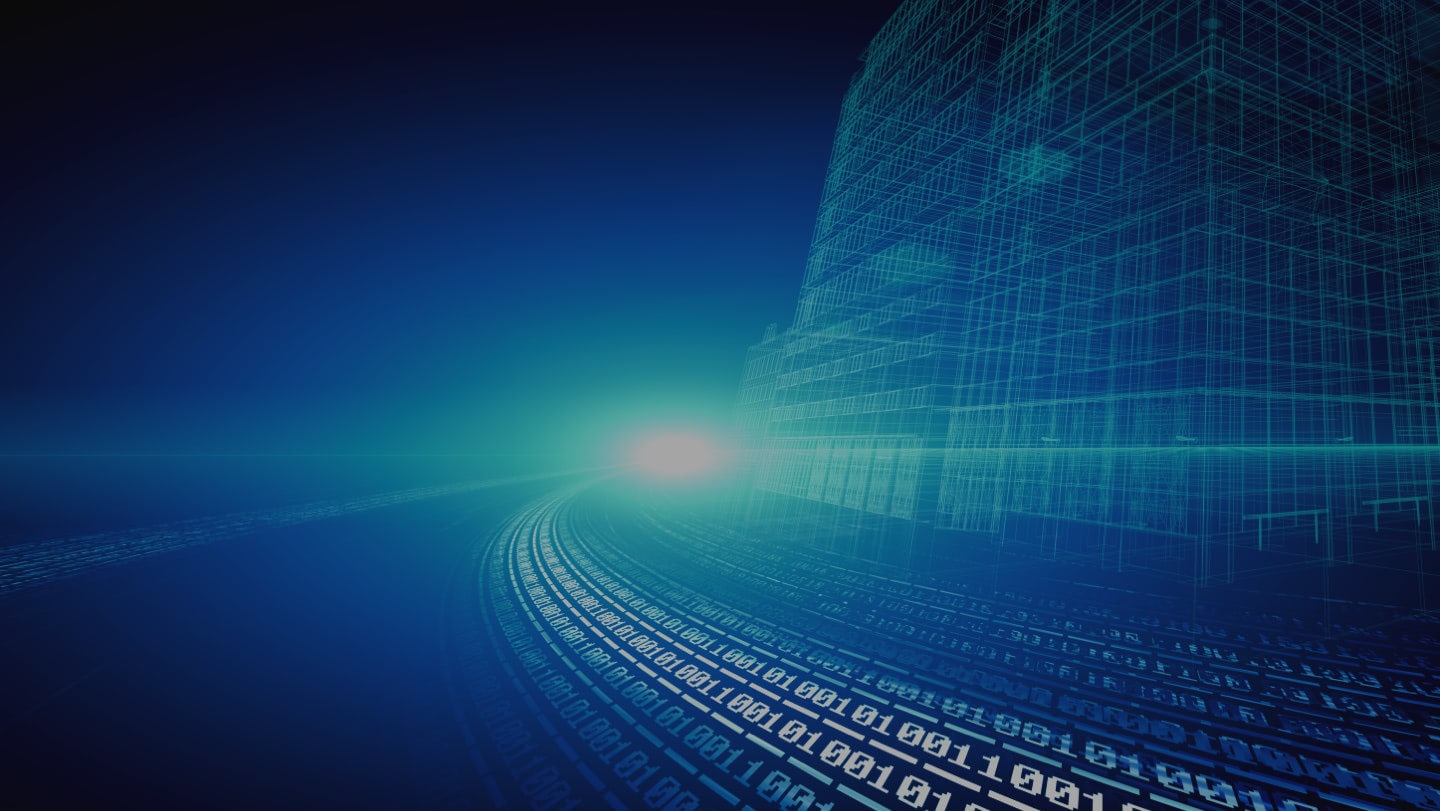
Berkshire Grey Blog
Debunking Tilt-Tray Myths: Why Robotic Sortation is the Future of Efficient Logistics
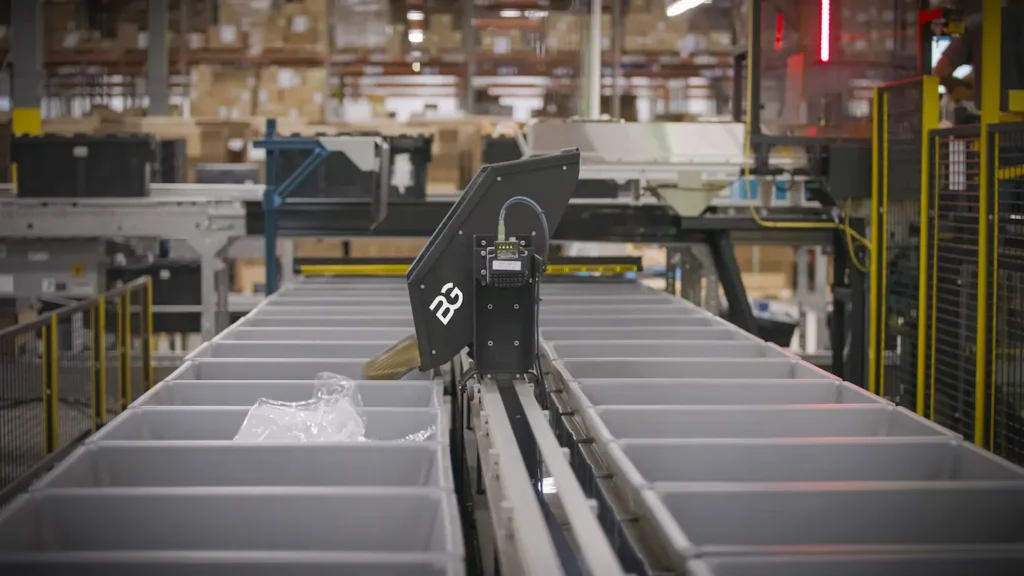
Debunking Tilt-Tray Myths: Why Robotic Sortation is the Future of Efficient Logistics
In today’s fast-paced logistics environment, aging unit sorters and traditional tilt-tray systems are becoming a liability. As noted by Noah Maynard, VP of Solutions Architects at Berkshire Grey, businesses using these legacy systems are often forced to deal with inefficiencies, limited SKU handling, and a rigid, fixed infrastructure that cannot scale with growing demand. During a recent webinar, Noah discussed the urgent need for advanced, flexible solutions that address these limitations and offer significant cost savings. This blog will explore the key takeaways from that session, debunk common myths about tilt-tray sortation, and showcase how Berkshire Grey’s robotic sortation systems are revolutionizing warehouse efficiency—unlocking millions in savings and future-proofing operations for years to come.
The Tilt-Tray Myth: Bigger Isn’t Always Better
Myth #1: Traditional Unit Sorters Are a One-Size-Fits-All Solution
Reality:
Traditional tilt-tray systems, while efficient for certain applications, are designed for specific size, weight, and shape parameters. This rigidity limits their ability to handle a wide variety of SKUs, especially when dealing with oversized, irregular, or rolling items. BG robotic sortation systems, by contrast, are built with advanced sensors and adaptable software, offering nearly 100% SKU coverage. Whether it’s handling bulky coats, delicate cosmetics, or unbagged apparel, our robotic sortation flexes to meet the unique needs of each item.
Case in Point:
A major Fortune 100 retailer faced challenges with its aging tilt-tray sorter, struggling with limited SKU handling and frequent manual exceptions. By switching to Berkshire Grey’s robotic system, the retailer achieved a 97% SKU coverage, drastically reducing manual interventions and streamlining operations.

Myth #2: High Efficiency Comes at the Cost of Flexibility
Reality:
Tilt-tray sorters are often seen as the gold standard for high throughput. However, this efficiency comes with a trade-off: they are designed with a fixed infrastructure, making it difficult to scale up or reconfigure as business needs change. As your product mix evolves, tilt-tray systems can become a bottleneck rather than a facilitator.
BG robotic sortation systems shine in their modular design. With scalable building blocks, they allow for seamless expansion without major disruptions. Whether you’re experiencing seasonal peaks or long-term growth, robotic systems adapt to changing demand with ease.
Customer Success:
One of Berkshire Grey’s clients needed to ramp up capacity during peak seasons. With a modular robotic sortation setup, they were able to scale their system quickly, increasing throughput by 15% without expanding their physical footprint.
Myth #3: Robotic Sortation Systems Require Extensive Facility Modifications
Reality:
A common misconception is that implementing a robotic sortation system requires significant changes to your existing facility. Traditional tilt-tray sorters often need a large, dedicated space with extensive structural modifications. In contrast, BG robotic sortation systems are designed to fit within existing brownfield environments, even utilizing mezzanine spaces.
This flexibility not only reduces installation time but also minimizes disruptions. In many cases, robotic sortation systems can be integrated alongside existing operations, enabling a smoother transition.
The Problem with Downtime: Single Points of Failure
Traditional unit sorters are known for their efficiency but can suffer from a major flaw: a single point of failure. When one component breaks, the entire system halts, causing costly downtime. Robotic sortation systems, however, are designed with distributed reliability. With multiple independent modules, even if one component requires maintenance, the rest of the system continues operating, ensuring nearly uninterrupted throughput.
Example: In a recent deployment, Berkshire Grey’s robotic system replaced an outdated tilt-tray sorter for a large retailer. The old system experienced frequent breakdowns, leading to hours of lost productivity. The new robotic system, with its distributed design, maintained over 98% uptime, even during maintenance activities, significantly boosting overall warehouse productivity.

Busting the Labor Myth: Robots Replace Jobs
Reality:
Contrary to popular belief, robotic sortation doesn’t eliminate jobs—it transforms them. Instead of requiring a large workforce for manual tasks like induction and pack-out, robotic systems streamline these processes, allowing employees to focus on higher-value activities. This shift not only reduces labor costs but also enhances job satisfaction.
In fact, many warehouses report improved employee retention after implementing robotic systems. The work is less physically demanding, and the intuitive user interfaces make onboarding easier, even for temporary staff.
Customer Feedback:
One operator at a Berkshire Grey deployment site described it as the best job they’ve ever had in the distribution center, citing reduced strain and easier tasks. Another employee delayed retirement because the new system made their job more manageable and enjoyable.
Reducing the Cost per Unit: The ROI of Robotic Sortation
For businesses evaluating whether to replace their aging tilt-tray sorter, the cost can be daunting. However, simply reinvesting in the same traditional technology often offers little in terms of a return on investment. Robotic sortation systems, on the other hand, provide significant labor and space savings, delivering faster ROI—sometimes in less than a year.
Consider This:
A head-to-head comparison between a new tilt-tray sorter and Berkshire Grey’s robotic system revealed stark differences. The robotic system reduced the cost per unit from 91 cents to just 29 cents, while also increasing the facility’s capacity by 10%. Over time, these savings can add up to millions of dollars, transforming your bottom line.
Debunking the Myth of Complex Maintenance
Reality:
Another misconception is that robotic systems require a specialized maintenance team with advanced skills. In truth, the maintenance needs of robotic sortation systems are often simpler than those of traditional sorters. Existing maintenance staff can easily handle routine tasks like greasing motor ports and cleaning components.
This approach not only reduces maintenance costs but also empowers your current workforce, providing them with new skills and increasing job satisfaction.
Integration Made Simple: Seamless Compatibility with Existing Systems
Warehouse managers often worry about integrating new technology with their existing warehouse management systems (WMS). However, robotic sortation solutions like those from Berkshire Grey are designed to be plug-and-play, simplifying the integration process.
Moreover, robotic systems offer enhanced data visibility, providing granular insights into order accuracy, item tracking, and real-time performance metrics. This additional data can be leveraged for predictive analytics, enabling even greater operational efficiency.
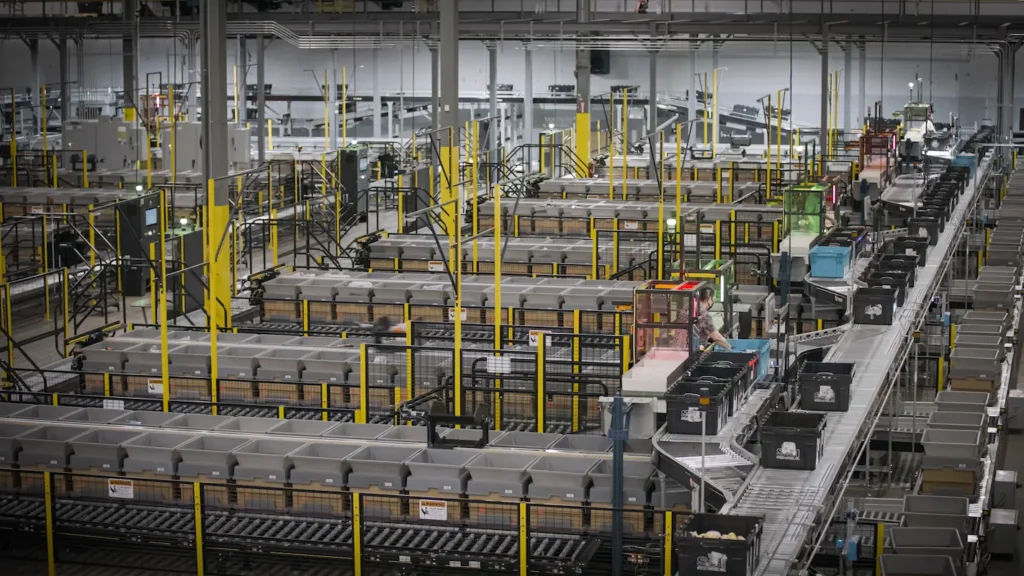
Peak Performance: Handling Seasonal Surges with Ease
Seasonal demand spikes are a challenge for any distribution center. Traditional sorters often struggle to keep up, requiring additional staffing and overtime. Robotic sortation systems are built to handle these fluctuations, dynamically adjusting to meet high demand without sacrificing performance.
With intelligent software orchestration, robotic sortation systems can scale their labor requirements based on real-time demand, ensuring that you’re always operating at peak efficiency.
Future-Proofing Your Warehouse: A Smarter Investment
In a world where technology is rapidly advancing, investing in a future-proof solution is crucial. Robotic sortation systems are built with scalability and adaptability in mind. They can easily integrate new software updates, leverage advancements in AI and machine learning, and adapt to changes in your product mix and order profiles.
The Bottom Line:
If you’re considering reinvesting in a traditional tilt-tray sorter, take a moment to explore your options. Robotic sortation offers not just a replacement, but a significant upgrade in terms of efficiency, flexibility, and long-term value. By making the switch, you can unlock millions in savings, improve employee satisfaction, and future-proof your operations against an ever-changing market landscape.
In conclusion, the myths surrounding tilt-tray sortation are just that—myths. Modern robotic sortation systems provide a compelling alternative, delivering superior performance, unmatched flexibility, and a faster ROI. The choice is clear: embrace innovation and lead your warehouse into the future.
Ready to learn more?
Contact Berkshire Grey today for a personalized consultation and discover how our robotic sortation solutions can revolutionize your operations.
Related Articles
Discussion on Robotic Sortation: Key Questions Answered
In a recent webinar, “Unlock $20M Savings with Superior Efficiency: Robotic …
Building on Momentum: Berkshire Grey Welcomes Dave Paratore as CEO
With a strong foundation of AI-driven robotics and a mission to …
The Future of Warehouse Automation: A Deep Dive into Robotic Put Wall Systems
During our recent webinar titled “Automate and Accelerate: Replacing Pick-to-Light with …
Get Started
with Berkshire Grey
Contact the BG Fulfillment Automation Sales Engineering Team to Learn How to:
- Reduce operations expense by up to 70%.
- Lessen your dependency on labor.
- Bolster facility throughput by up to 25% to 50% with automation.
- Get a customized ROI analysis of your specific environment and business.
Call +1 (833) 848-9900
or connect using our form.