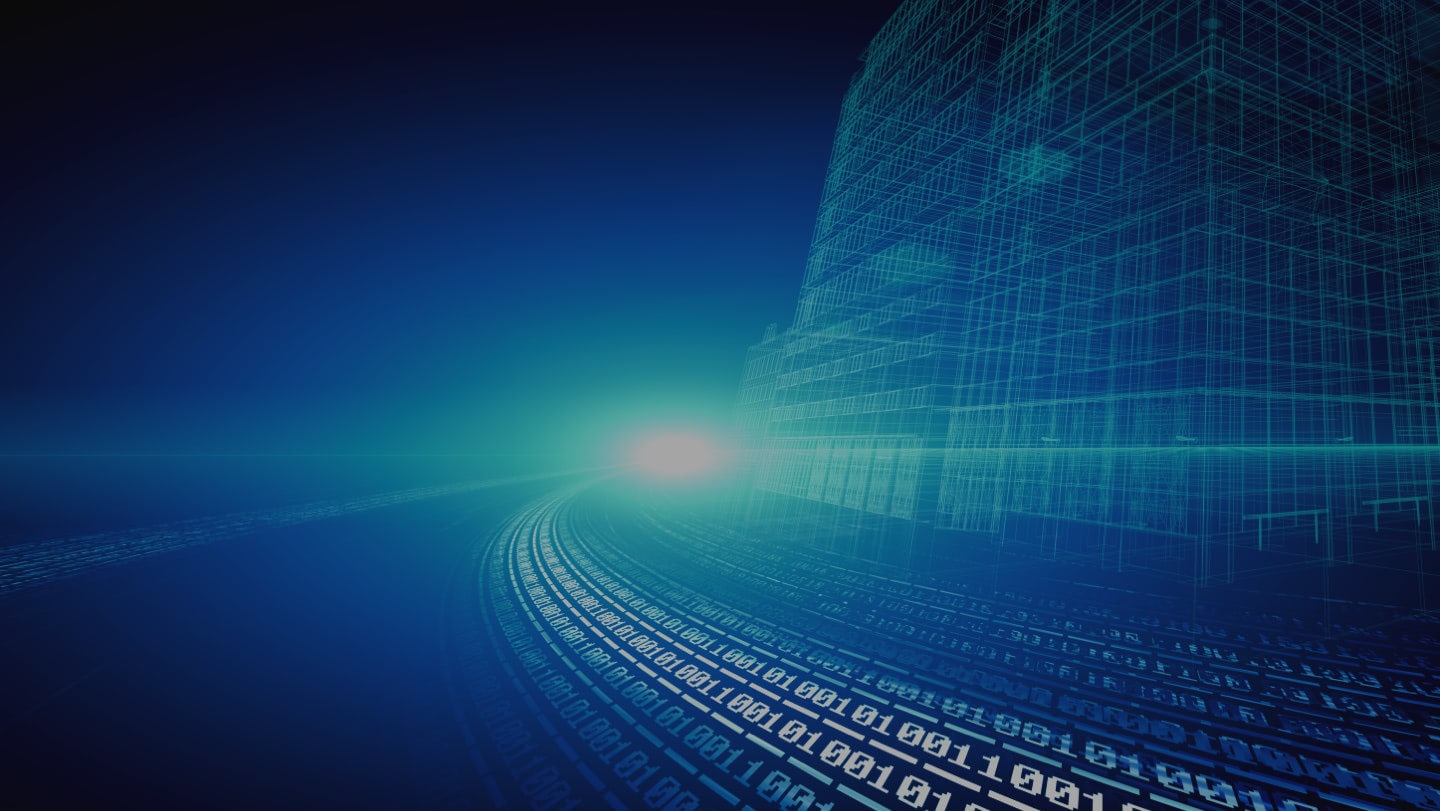
Berkshire Grey Blog
Discussion on Robotic Sortation: Key Questions Answered
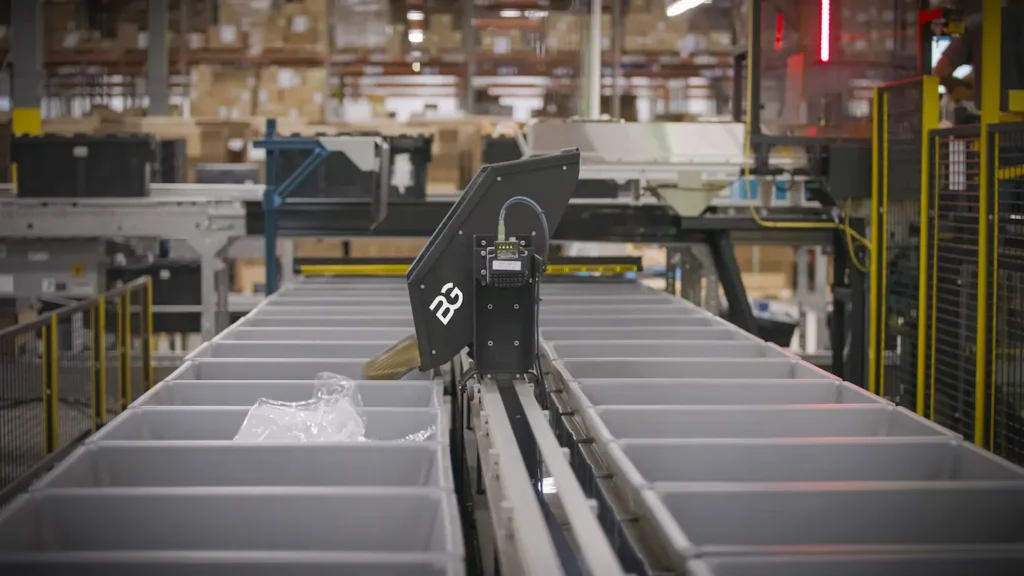
Discussion on Robotic Sortation: Key Questions Answered
In a recent webinar, “Unlock $20M Savings with Superior Efficiency: Robotic Sortation vs. Traditional Unit Sorters”, hosted by Berkshire Grey, attendees explored the transformative potential of robotic sortation systems. This dynamic discussion, led by Noah Maynard, Vice president of Solutions Architects at Berkshire Grey, delved into the challenges of traditional unit sorters and highlighted how robotic solutions address these pain points while unlocking efficiency and savings. Below, we expand on some of the key questions from the session, providing in-depth insights into this cutting-edge technology.
1. Can a robotic sorter manage packaging?
Yes, robotic sorters are highly capable of managing packaging operations. Berkshire Grey’s robotic sortation system integrates sophisticated software with advanced hardware to streamline packaging workflows. The system uses orchestration software to ensure that cartons are routed to the correct stations at the right time, reducing the need for manual intervention.
During the session, Noah emphasized that the system is optimized for a wide range of SKUs, ensuring precise sorting and packaging into containers or boxes. The system’s adaptability is especially beneficial for complex environments, such as retail and e-commerce, where items vary significantly in size, shape, and material. Furthermore, the system’s ability to dynamically route and adjust based on demand profiles ensures that packaging remains efficient even during peak periods.
2. Can you manage packing rectangular items in the same shipping carton to maximize cube utilization?
Certainly. Berkshire Grey’s robotic sortation systems are designed to maximize box fullness, a critical factor in reducing shipping costs and improving sustainability. The system utilizes advanced sensors and automatic ejection mechanisms to monitor box weight, capacity, and configuration. Items are sorted above the height of the box, allowing for maximum cube utilization while avoiding overloading.
Noah elaborated on how the system includes features like jostling mechanisms to compact items and maximize packing density. Customers can also customize parameters, such as weight thresholds and cut-off times for box ejection, ensuring that each box meets operational requirements. For example, heavy items like hard goods are monitored to ensure they do not exceed ergonomic or safety limits for handling. This approach not only minimizes “shipping air” but also aligns with sustainability goals by reducing excess packaging.
3. Can you please talk about the uptime of your system?
The uptime of the Berkshire Grey robotic sortation system is a standout feature, effectively approaching 100%. This is achieved through its modular design, which eliminates the risk of single points of failure that are common in traditional unit sorters. If one module experiences an issue, the system continues to function with minimal disruption, maintaining up to 98–99% of throughput capacity.
Noah emphasized that this distributed reliability is crucial, particularly during peak demand periods. The system’s design ensures that individual shuttles or components can be serviced or maintained without halting the entire operation. This resilience reduces downtime, enabling warehouses to maintain productivity even when minor issues arise.
4. Can you address typical maintenance activities and costs?
Maintenance for the Berkshire Grey system is straightforward and aligns with the skills of existing warehouse maintenance teams. The system’s design minimizes moving parts, which simplifies upkeep and reduces potential failure points. Typical tasks include greasing motor ports, inspecting conveyor belts, and cleaning components such as slides.
During the session, Noah highlighted that these activities do not require specialized skills, making it easy for businesses to transition without hiring additional technical staff. Maintenance costs are predictable and comparable to those of traditional systems, allowing companies to factor them into their long-term budgets with confidence.
5. How long does it take to install the entire system in a warehouse, brownfield or greenfield?
Installation of the Berkshire Grey system is designed to be efficient and minimally disruptive. In most cases, the entire system can be operational within three months. This rapid deployment is facilitated by the system’s modular design, which allows for off-site assembly and quick on-site integration.
For brownfield sites, where existing operations must continue uninterrupted, the system’s flexibility shines. Components can be installed in phases, allowing businesses to gradually transition while maintaining productivity. For greenfield sites, the process is even faster, as the system can be optimized for the new layout from the start. Minimal facility modifications, such as leveling floors and installing standard conveyors, are required, further reducing installation time.
6. How future-proof is your technology? Can it evolve with advancements in AI, machine learning, and predictive analytics?
The Berkshire Grey system is designed to evolve alongside advancements in technology, making it highly future-proof. Its modular hardware can accommodate component upgrades, while its software is continuously updated to improve functionality and adapt to new use cases.
Noah detailed how the system leverages AI and machine learning to analyze order profiles and optimize operations in real-time. This adaptability ensures that businesses can stay competitive as customer demands and market conditions evolve. Additionally, the system’s ability to collect and analyze granular data—such as timestamps and item-specific information—enhances its utility for predictive analytics and continuous improvement.
7. How do you know if robotic sortation is for you?
Robotic sortation systems are an excellent choice if your operation faces challenges such as high SKU variability, labor shortages, or the need to improve space utilization and throughput. If you are considering reinvesting in traditional unit sorters, Noah stressed the importance of exploring modern alternatives like Berkshire Grey’s systems.
These systems offer significant advantages, including reduced labor dependency, enhanced scalability, and improved ROI. For example, businesses transitioning from manual or traditional systems can achieve up to a 60% reduction in labor requirements while increasing throughput and SKU coverage. By evaluating your operational goals and constraints, you can determine whether robotic sortation aligns with your needs and offers the transformative value your business requires.
Conclusion
The webinar showcased how robotic sortation systems are revolutionizing fulfillment operations, offering enhanced efficiency, scalability, and ROI. Adopting advanced solutions like Berkshire Grey’s can provide the edge needed to thrive.
If you’re considering automation, take the time to explore how robotic sortation could fit your operation. By leveraging cutting-edge technology, you can not only address today’s challenges but also future-proof your business for years to come. Contact Berkshire Grey to learn more and take the next step in transforming your warehouse operations.
Ready to learn more?
Contact Berkshire Grey today for a personalized consultation and discover how our robotic sortation solutions can revolutionize your operations.
Related Articles
Why Robot Hands Won’t Take Over the Warehouse Anytime Soon
Will robot hands take over the warehouse? Of course not! Vacuum …
Building on Momentum: Berkshire Grey Welcomes Dave Paratore as CEO
With a strong foundation of AI-driven robotics and a mission to …
Debunking Tilt-Tray Myths: Why Robotic Sortation is the Future of Efficient Logistics
In today’s fast-paced logistics environment, aging unit sorters and traditional tilt-tray …
Get Started
with Berkshire Grey
Contact the BG Fulfillment Automation Sales Engineering Team to Learn How to:
- Reduce operations expense by up to 70%.
- Lessen your dependency on labor.
- Bolster facility throughput by up to 25% to 50% with automation.
- Get a customized ROI analysis of your specific environment and business.
Call +1 (833) 848-9900
or connect using our form.