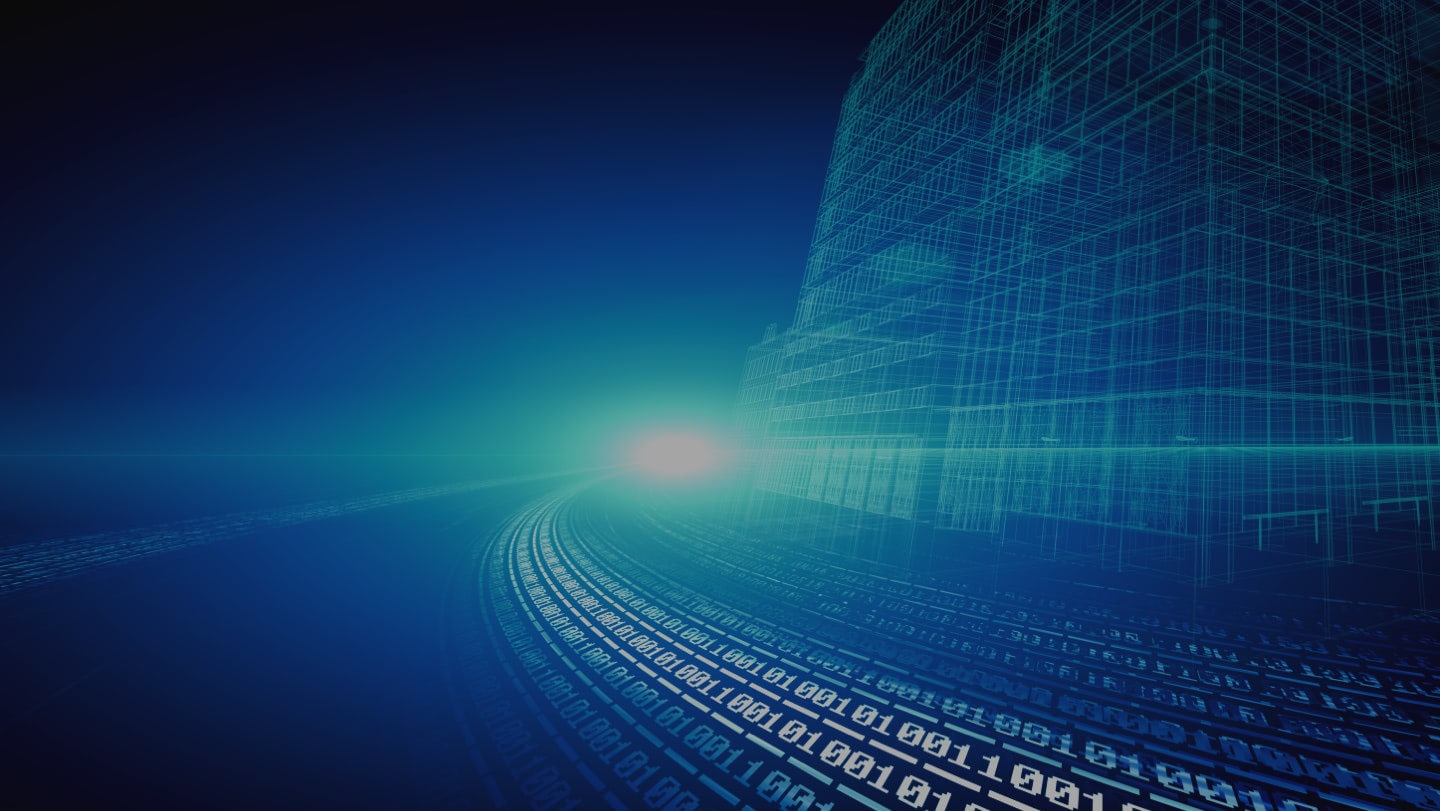
Berkshire Grey Blog
The Future of Warehouse Automation: A Deep Dive into Robotic Put Wall Systems

The Future of Warehouse Automation: A Deep Dive into Robotic Put Wall Systems
In today’s fast-paced e-commerce and retail environments, the need for efficient, scalable, and cost-effective warehouse automation solutions has never been greater. As traditional Pick-to-Light (PTL) systems approach the end of their lifecycle, many organizations face escalating maintenance costs and stagnating productivity. During our recent webinar titled “Automate and Accelerate: Replacing Pick-to-Light with the Next Generation of Automation,” our in-house expert and VP, Solutions Architects, Noah Maynard and one of our featured partners, Kyle Brock, VP of Advanced Technologies of S&H Systems shared insights on how robotic put wall systems are revolutionizing warehouse operations.
Let’s delve into the key points to understand how these systems can transform your operations.
The Evolution from Pick-to-Light to Robotic Put Walls
Ten to fifteen years ago, PTL was a remarkable technology. It increased throughput and productivity significantly, making it ideal for retail distribution. However, as e-commerce exploded, the need to pick items for fulfillment from the same areas introduced the concept of put walls. These systems allowed for efficient item sorting and order fulfillment without remodeling entire warehouses.
Imagine buying a car ten years ago. You’d expect a CD player, heated seats, and power windows. Today, those features are standard, and you’re looking for lane assist, adaptive cruise control, and a host of other advanced features. The same principle applies to warehouse automation. PTL systems that once seemed revolutionary now feel outdated, and the costs of maintaining these systems often exceed the benefits.
Companies are finding that upgrading their existing PTL systems is costly and offers no additional productivity gains. It’s like spending the same amount of money for an outdated car when you could get a modern, feature-rich model for the same price.
The Compelling Case for Robotic Put Walls
The critical issue is the need for investment to maintain operations. Will you invest in the outdated platform with no ROI, or choose the new platform that delivers greater value? With comparable capital expenditure, robotic put walls provide sorting three times faster, cover more SKUs, enable a more rapid deployment, and support scalable business growth.
The transition to robotic put walls isn’t just about keeping up with technology but about making a strategic investment that promises substantial returns. Here’s a closer look at the benefits:
- Labor and Space Efficiency: Robotic put walls deliver up to three times the labor savings and use only 25% of the space, compared to manual put walls.
- Minimal IT Impact: These systems are designed to be plug-and-play, minimizing disruptions to existing IT infrastructures, and ensuring rapid payback.
- High Reliability and Easy Maintenance: With fewer moving parts, these systems require minimal maintenance, leveraging the existing skill set of the maintenance team.
- Enhanced Productivity: Customers have reported up to 40% batch pick efficiency gains, driving significant improvements in overall warehouse productivity.
Real-World Success Stories
“We have seen tremendous success with these systems in real-world applications. For instance, an online retailer achieved a 20% direct labor savings in fulfillment, translating to 112 fewer staff hours per day and almost two cents saved per unit.” – Noah Maynard.
Another fashion retailer, sorting unbagged apparel through the system, transitioned from discrete to robotic batch picking, saved $403,000 annually and reduced labor hours by 117,000. This transition from zero to 100 resulted in significant savings of 32 cents per unit.
These examples underscore the tangible benefits of adopting robotic put walls, highlighting not only the operational efficiencies but also the significant cost savings that can be achieved.
One notable case involved a major beauty products retailer facing a $10 million investment to upgrade their aging PTL system. This upgrade would only maintain their current productivity levels without offering any new efficiencies. By switching to Berkshire Grey’s robotic put wall system, the retailer was able to triple their sorting speed and handle a diverse range of SKUs more efficiently. This transition not only avoided the hefty upgrade costs but also resulted in significant operational savings and a rapid return on investment.
Driving Efficiencies Throughout the Warehouse
The implementation of robotic put walls extends far beyond merely enhancing the sorting process; it drives significant efficiencies throughout the entire warehouse operation. One of the most remarkable benefits is the potential to achieve 30 to 40% batch pick efficiencies. This substantial improvement arises from the increased number of destinations available with the robotic put wall solution, enabling larger batch sizes. With three times the destinations compared to traditional systems, operations can streamline their picking process, reducing travel time and significantly increasing throughput.
At the heart of this system’s efficiency is its operational workflow. Operators simply scan and induct items onto a belt, much like a grocery store clerk. This simplicity is key to reducing training time and minimizing errors. Once inducted, the robotic carrier takes over, sorting items into outbound destinations with precision. A customer site with six of these put walls integrated with conveyors showcases this efficiency in action. Items are sorted into cubbies, highlighting the system’s ability to handle a diverse range of SKUs, including rolling items, unbagged apparel, and boxed shoes.
Some standard features make the put walls particularly effective. The cog belt, for instance, allows for the induction of round items, which is especially beneficial in industries like Health and Beauty Supply, where product shapes can vary significantly. The increased number of cubbies per put wall also dramatically enhances batch pick efficiency. When the number of destinations in a single put wall doubles or triples, it leads to greater density and reduced travel time during picking. This improvement means operators can pick multiple items of the same SKU at the same stop, significantly boosting overall efficiency.
In traditional manual operations, there is often a trade-off between batch pick efficiencies and put wall efficiencies. For example, a manual put wall with 2,000 destinations might offer better batch picking, but it sacrifices speed and efficiency on the put side. The robotic put wall system eliminates this trade-off by offering the best of both worlds. Put operators no longer need to walk, as the system handles the sorting, thereby increasing speed and efficiency. Additionally, the enhanced batching capabilities drive efficiencies back to the pick area, making the entire operation more streamlined and productive.
Overcoming Implementation Challenges
Let’s address common concerns about barriers to entry and integration challenges. One critical factor is ensuring that the put wall system is conducive to the existing order profile. Additionally, internal IT resources must be evaluated to determine if they can handle the integration or if external assistance is needed.
“Implementing a new solution can be daunting, especially for companies transitioning from zero automation. However, robotic put walls are designed to be appetizing and attainable, even for operations without existing automation. The key is understanding your current order profile and IT resources to ensure a smooth transition.” – Kyle Brock.
The flexibility of robotic put walls makes implementations very fast and modular. For example, we can set up a robotic put wall at a trade show within a day. In a warehouse, we typically start by installing initial capacity, then do a rolling implementation to gradually decommission old systems.
Addressing Specific Use Cases
During the Q&A session, attendees asked about specific use cases, such as handling auto parts. Noah explained that the robotic put wall system is designed for a wide range of SKUs, including oddly-shaped and cylindrical items. The system can handle weights up to 10-12 pounds, making it versatile for various industries.
One of the value drivers of the BG system is SKU coverage, allowing one process to handle as much volume as possible. This flexibility is crucial for industries like auto parts, where items can vary significantly in shape and size.
The Road Ahead
As warehouse operations continue to evolve, the importance of adopting advanced automation solutions becomes increasingly evident. The discussion concluded with a reflection on the broader implications of these technologies.
“It’s all about making informed decisions. If you’re going to spend the same amount of money today that you did ten years ago, why settle for outdated technology? By investing in robotic put walls, you’re future-proofing your operations and gaining a competitive edge.” – Kyle Brock.
Automation is not just about replacing manual processes but enhancing overall efficiency and productivity. With robotic put walls, you’re not only reducing costs and improving accuracy but also positioning your business for long-term success.
In conclusion, the webinar highlighted the critical role of robotic put wall systems in modernizing warehouse operations. The compelling case for these systems lies in their ability to deliver substantial labor and space savings, minimal IT impact, high reliability, and significant productivity gains. Real-world success stories further validate these benefits, showcasing how businesses can achieve remarkable efficiency and cost savings.
As we move forward, embracing these advanced automation solutions will be key to staying competitive in the dynamic e-commerce and retail landscapes. Investing in robotic put walls is not just a technological upgrade; it’s a strategic move towards a more efficient, scalable, and sustainable future.
Related Articles
Why Robot Hands Won’t Take Over the Warehouse Anytime Soon
Will robot hands take over the warehouse? Of course not! Vacuum …
Discussion on Robotic Sortation: Key Questions Answered
In a recent webinar, “Unlock $20M Savings with Superior Efficiency: Robotic …
Building on Momentum: Berkshire Grey Welcomes Dave Paratore as CEO
With a strong foundation of AI-driven robotics and a mission to …
Get Started
with Berkshire Grey
Contact the BG Fulfillment Automation Sales Engineering Team to Learn How to:
- Reduce operations expense by up to 70%.
- Lessen your dependency on labor.
- Bolster facility throughput by up to 25% to 50% with automation.
- Get a customized ROI analysis of your specific environment and business.
Call +1 (833) 848-9900
or connect using our form.